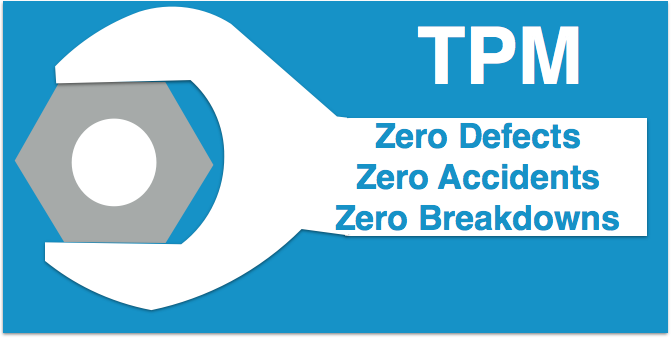
Five Reasons Why People Like TPM Program
Uninterrupted production without any kind of mishaps, hold ups or faults certainly seems like a dream come true. However, you try to achieve this utopian state by implementing the TPM Program for your own business. You would find it to be totally worthwhile once you understand the principles involved. First things first though; you need to check out what the program involves before going on to experiment with it and eventually taste success.
The acronym can be expanded to ‘total production maintenance’ where you aim high to keep the weak links out. In short, it is a process that plans for ‘perfect production’ with absolutely nothing coming in the way. In other ways you hope to progress with no defects, no flaws, no interruptions and no accidents. Your ambition is definitely high for every production comes with its own drawbacks.
However, experts have proved that such a scenario can be achieved by starting on a proactive maintenance of the equipment in use as well as the systems that also includes checking, repairing and replacing the faulty parts or entire equipment well in time before it holds up the production line. It cannot be done in a single day though. The staff dealing with the process needs to be trained properly as well. Fortunately, you would be able to achieve near perfect production by means of implementing TPM measures ultimately. It makes sense to begin ASAP. So, go for it but you do need to look at the advantages that the program will provide you with.
Table of Content
Scheduled & Collective Maintenance Programs
The employees happen to play the most important role during the production process. TMP is concerned with empowering the employees so that each of them handles his/her pat with no questions asked. This helps in reducing the time for cleaning and maintenance of the equipment with no chances of receiving a rude shock with a part or an entire machine suddenly becoming nonfunctional. The TPM Rota includes all the employees of the concerned plant with each of them being delegated a certain task pertaining to the maintenance of the systems. There is no requirement of asking for external assistance therefore with the employees taking a keen interest in their work and fulfilling their responsibilities perfectly. Statistics have revealed that the reduction of unplanned maintenance work can be as high as 98% once TPM is implemented successfully.
Measuring Results
The initial goal of achieving flawless production is measured by means of “Overall Equipment Effectiveness (OEE).” This happens to be standard for checking all-round productivity of a unit, both in terms of specific production procedures as well as the obscure factors involved. OEE is obtained in the form of a numeric data. The data thus received can help a company to identify its loss making areas, rate the progress and test the efficacy of the equipment employed, all at the same time. Comparing the standards with that of the concerned industries success stories becomes easy as a result. Improvement becomes simple as well when backed by data.
Improved Output
Proper and preventive maintenance happens to be the key of ‘total production maintenance.’ With no sudden breakdowns and loss of man hours, production goes on smoothly and effectively showing improvement with almost every cycle. OEE helps to point out the weaknesses within the system as well and the management can try to reduce the gaps by setting up specific check points in the production line thereby noting the discrepancies and rectifying the mistakes immediately. This is sure to cause a dwindling of the negative points until the much hoped for perfect production is achieved. Since the faults can be discovered at the earliest there is almost no reworking to be done and the employees are happy to obtain the much deserved kudos from the management.
Workplace Safety
The TPM Program modules rests on eight pillars of success with safe working environment being of prime importance. The program remains focused on keeping the workplace neat, clean and totally organized in order to minimize faults. There is less chance of forgetting important tasks as a result or beginning work haphazardly that might end in wastage of time. Inspection and cleaning plus lubrication of machinery happen to be one of the chief foundations of TPM. With every employee taking care to maintain and clean the equipment that he uses, there is no instance of breakages, leaky lubricants or fuel as well as faulty execution due to the buildup of grime on the overused machine parts. Workplace accidents are definite to become a rarity once the program gets to be implemented fastidiously. Keeping one’s work area organized can help in reducing the risk factors substantially too. A dirty workstation with the tools not k in their proper places can cause much anxiety with temper flare ups and wastage of time. Concentration is affected adversely as well causing one to make mistakes thereby compromising the productivity of the entire office. The activities related to TPM enable the employees to avoid clutter and prevent mishaps thereby ensuring workplace safety.
Equal Participation
While TPM sounds to be a great solution on paper, implementing it properly can pose a challenge. The pillars of the program can be achieved only when there is a general consensus with the workers willing to change their notions about work. Sure, imparting the required knowledge and training the staff can make a world of a difference yet it is important to make the employees take pride in their work and aspire hard for improved productivity. However, it would be impossible to have the employees take ownership of their tasks without giving them a voice. While, repairing, maintaining and replacing the essential equipment can help to up the ante, participation of all members of the staff is of equal importance. The best way to ensure this would be to listen to their grievances and sort out the problems, making them feel that they are a part of the company. Employee recognition in the form of rewards may help in encouraging active participation in TPM programs as well